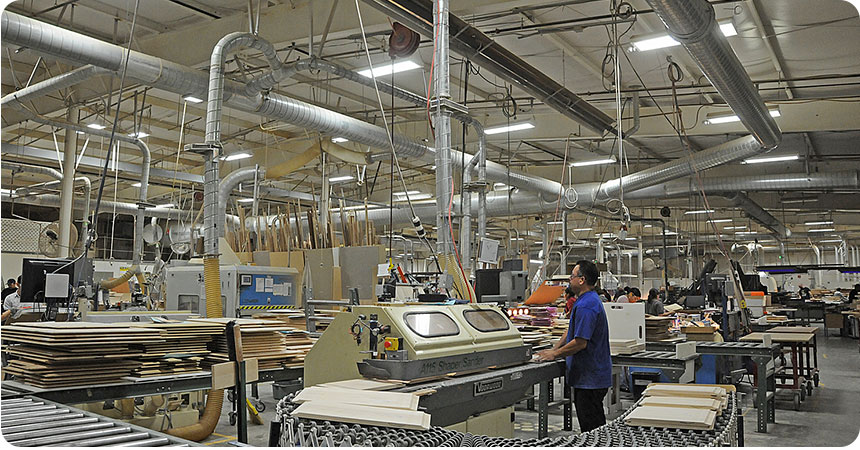
Sawdust, a byproduct of wood products manufacturing, adds debris and dust particles to the shop floor if not effectively managed with industrial-sized dust collectors. Rather than invest capital in more energy-intensive equipment, Brentwood Corporation installed an on-demand ventilation system to control dust, eliminating the need for new collection equipment and saving nearly one-third of the plant’s annual energy use in the process.
Located in Molalla, Oregon, the kitchen cabinet door maker’s big dust collectors and fans accounted for half of its electrical usage. Growth in production had pushed their existing system to capacity, prompting the company to consider purchasing more equipment to manage chips and dust.
“Another dust collector would have done the job, but it would have increased our energy consumption,” said Dan Wagner, plant engineering manager and maintenance manager, Brentwood Corporation. “We could have spent up to $150,000 per year on energy alone for the additional dust collector.”
Brentwood installed the EcoGate® On-Demand Ventilation System, which improves the capability and energy efficiency of the plant’s existing dust collectors. With approximately 30 percent of the plant’s equipment actually producing sawdust at any given time, the ventilation system senses when airflow is or isn’t needed and uses a series of automated gates to direct capacity to other workstations in use.
The system includes three new variable frequency drives, VFDs, for existing fans, and one new master control station to communicate with the three VFDs, which controls when to open and close gates. In total, the master controller communicates with sensors and gauges on 100 individuals gates. Brentwood now has room for additional pieces of equipment in the plant at limited additional energy cost.
“With the system overtaxed, we couldn’t completely eliminate a light dust haze in the air. Now, each active machine is extracting more air and capturing the dust even better than we did before. Less dust means cleaner indoor air for our employees,” explained Wagner.
In addition to decreased energy consumption, Brentwood’s ventilation system delivers other benefits. The new VFDs reduce wear and tear on the fan belts and bearings to ease future maintenance costs, and reduce noise levels to improve the work environment for employees.
Energy Trust provided Brentwood with cash incentives of over $257,600, which covered nearly 50 percent of the project’s upfront cost. Overall, the manufacturer estimates it will save more than 1.3 million kilowatt hours of electricity in energy consumption and approximately $86,000 in energy costs annually.