A quick glance in your trash or recycling bin is all it takes to see the huge role single-use plastics play in American lives. Even a few takeout meals add up quickly, and those to-go containers, utensils, straws and cups affect the environment long after your food is a distant memory.
After spending decades in plastics manufacturing, Chris Vitello, founder and CEO of Atacama Manufacturing, couldn’t shake the feeling that instead of contributing to the problem, he could be part of the solution.
“In 2009 I looked back over my career and said, ‘Boy, I have personally sent a lot of plastic to the landfill.’ That’s when I decided there had to be a better way, and I started what is now Atacama Manufacturing.”
The Albany-based company aims to break the waste cycle by replacing single-use plastics with plant-based, reusable and compostable packaging. It also works with customers like the restaurant chain Sweetgreen to fine-tune a circular reuse system. Through this process, Atacama makes plant-based containers, collects them after use, and turns the used products into raw material for new ones — repeating the cycle in a closed loop instead of sending the containers to a landfill.
“We’ve been able to build an organization based on innovation, where we’re constantly pushing the forefront of technology to enable better environmental situations,” said Vitello.
It’s a good time to be a U.S.-based manufacturer, too. As the global supply chain has taken hits from the COVID-19 pandemic, demand is surging for locally and regionally made packaging.
“We’ve had the phone just ringing off the hook with people that want to manufacture in the U.S. or want to reduce their environmental impact,” said Vitello. Atacama has been able to grow to meet that need thanks to new equipment and incentives from Energy Trust of Oregon, which helped the company upgrade its 18,000-square-foot production facility.
Atacama’s manufacturing plant was originally built in the 1980s. When the company set up operations, the facility had hundreds of old fluorescent lights inside, outdated mercury-vapor lighting outdoors and a 30-year-old compressor with leaking air lines that needed to be replaced.
Before the pandemic, these issues weren’t urgent because about 80% of Atacama’s business came from distributing green packaging made elsewhere. But as international lockdowns led to shortages, Atacama’s business model switched to 80% manufacturing and 20% distribution. “The Energy Trust program was a perfect catalyst to get us to do the upgrade sooner rather than later,” said Vitello.
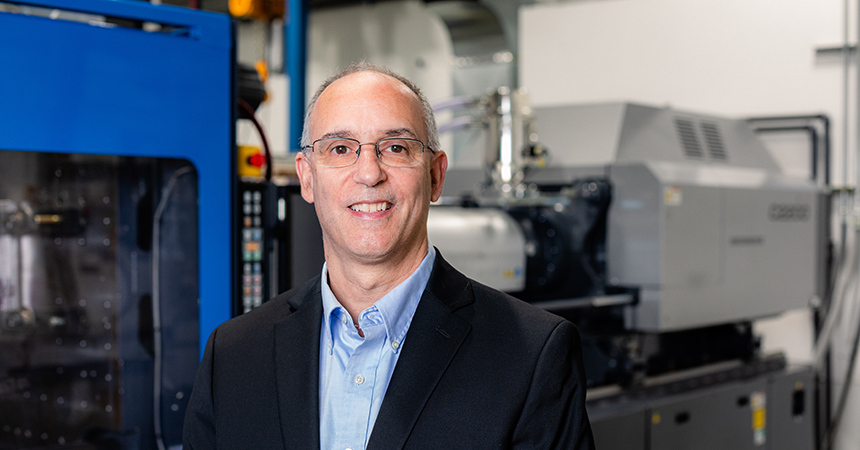
Atacama Manufacturing CEO Chris Vitello has partnered with Energy Trust for several energy-efficient upgrades. “It’s undoubtedly one of the best programs I’ve ever had to interact with,” he said. “It’s really done in an outstanding way.”
Pressurized air is critical for Atacama’s operations because it powers a lot of the equipment used to move and process raw materials during production. The state-of-the-art new compressor and air supply lines are safer, more efficient and better for the environment. And Atacama offset more than one-third of the cost by taking advantage of more than $10,000 in cash incentives for the upgrade.
“Overall, Energy Trust has done a great job of creating a process which is very user friendly,” said Vitello. “Like any small business owner, I was worried on the front end that I was too busy and just didn’t have time for this extra thing. But the contractor and Energy Trust made it very, very simple and easy to move forward. I would recommend it to anybody.”
Based on his positive experience with the compressor project, in 2020 Vitello also replaced old lighting systems with energy-efficient LEDs and received $13,600 in Energy Trust cash incentives for the lighting projects, offsetting the expense by nearly a third.
Overall, the upgrades also will save Atacama an estimated 150,300 kilowatt-hours in energy each year, lowering its carbon footprint and reducing its utility bills.
“It does require some investment,” said Vitello of the capital costs for the new equipment. “But the investment certainly has a payback. My advice would be for any small business to investigate it with either their contractor or their electrician. Run the numbers. More times than not, I would estimate that it pays for itself very, very quickly.”
The company plans to keep the momentum going, too. Its next big project: Installing rooftop solar panels to generate clean energy for the plant. “Long-term, we would love for our manufacturing operation to be basically zero carbon,” said Vitello.
“Being a company that focuses on environmentally friendly products, we want to do as much as we can in our manufacturing operations to be as environmentally friendly as possible. What I love about the program is that it’s good for your business and also good for the planet.”
Learn more about how Energy Trust can help upgrade the equipment for your industrial business at www.energytrust.org/for-business.
Basta con dar un vistazo a la basura o al cubo de reciclaje para darse cuenta del enorme papel que desempeñan los plásticos de un solo uso en la vida de los estadounidenses. Incluso unas pocas comidas para llevar se acumulan rápidamente, y esos envases, cubiertos, popotes y vasos para llevar afectan al medio ambiente mucho después de que la comida sea un recuerdo lejano.
Después de pasar décadas en la fabricación de plásticos, Chris Vitello, fundador y director general de Atacama Manufacturing, no pudo evitar la sensación de que, en lugar de contribuir al problema, podría ser parte de la solución.
“En 2009, reflexionando sobre toda mi carrera me dije: ‘Vaya, yo personalmente he enviado mucho plástico al vertedero’. Fue entonces cuando decidí que tenía que buscar una mejor manera de producir, y empecé lo que ahora es Atacama Manufacturing”.
La empresa, con sede en Albany, pretende romper el ciclo de los residuos sustituyendo los plásticos de un solo uso por envases de origen vegetal, reutilizables y compostables. También trabaja con clientes como la cadena de restaurantes Sweetgreen para poner a punto un sistema de reutilización circular. Mediante este proceso, Atacama fabrica envases de origen vegetal, los recoge después de su uso y convierte los productos usados en materia prima para otros nuevos, repitiendo el ciclo en un bucle cerrado en lugar de enviar los envases a un ?vertedero.
“Hemos sido capaces de construir una organización basada en la innovación, en la que impulsamos constantemente la vanguardia tecnológica para hacer posible mejores condiciones ambientales”, dijo Vitello.
A este contexto también se suma el hecho de que es un buen momento para ser un fabricante con sede en Estados Unidos. Dado que la cadena de suministro mundial se ha visto afectada por la pandemia del COVID-19, la demanda de envases fabricados a nivel local y regional está aumentando.
“El teléfono no para de sonar con gente que quiere fabricar en Estados Unidos o que quiere reducir su impacto ambiental”, dijo Vitello. Atacama ha podido crecer para satisfacer esa necesidad gracias a los nuevos equipos y a los incentivos de Energy Trust of Oregon, que ayudaron a la empresa a mejorar su planta de producción de 18,000 pies cuadrados.
La planta de producción de Atacama se construyó originalmente en la década de 1980. Cuando la empresa inició su actividad, las instalaciones tenían cientos de luces fluorescentes antiguas en el interior, una iluminación de vapor de mercurio anticuada en el exterior y un compresor de 30 años con fugas en los conductos de aire que debía ser sustituido.
Antes de la pandemia, estos problemas no eran urgentes porque cerca del 80% del negocio de Atacama procedía de la distribución de envases ecológicos fabricados en otros lugares. Pero cuando los cierres internacionales provocaron escasez, el modelo de negocio de Atacama pasó a ser un 80% de fabricación y un 20% de distribución. “El programa Energy Trust fue un catalizador perfecto para que hiciéramos la actualización más pronto que tarde”, dijo Vitello.
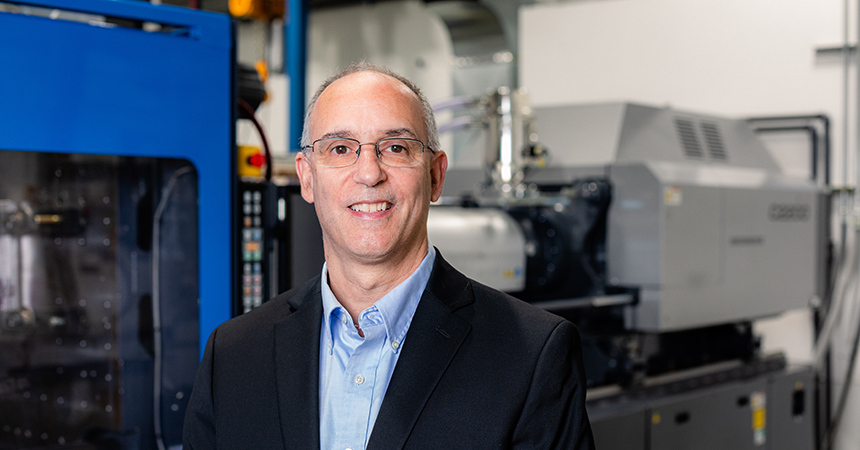
El director general de Atacama Manufacturing, Chris Vitello, se ha asociado con Energy Trust para realizar varias mejoras de eficiencia energética. “Sin duda es uno de los mejores programas con los que he tenido que interactuar”, dijo Vitello. “Realmente se ha hecho de una manera excepcional”.
El aire presurizado es fundamental para las operaciones de la fábrica, ya que alimenta gran parte de los equipos utilizados para mover y procesar las materias primas durante la producción. El nuevo compresor y las líneas de suministro de aire de última generación son más seguros, más eficientes y mejores para el medio ambiente. Atacama compensó más de un tercio del costo aprovechando más de $10,000 en incentivos en efectivo para la actualización.
“En general, Energy Trust ha hecho un gran trabajo al crear un proceso que es muy fácil de usar”, dijo Vitello. “Como cualquier propietario de una pequeña empresa, al principio me preocupaba estar muy ocupado y no tener tiempo para este proyecto adicional. Pero el contratista y Energy Trust lo hicieron muy sencillo y fácil de sacar adelante. Se lo recomendaría a cualquiera”.
Basándose en su experiencia positiva con el proyecto del compresor, en 2020 Vitello también sustituyó los antiguos sistemas de iluminación por LEDs de alta eficiencia energética a través de la oferta de iluminación sin coste de Energy Trust para pequeñas empresas, recibiendo $13,600 en incentivos para los proyectos de iluminación, compensando el gasto en casi un tercio.
En general, las mejoras también ahorrarán a Atacama unos 150,300 kilovatios-hora de energía al año, lo que reducirá su huella de carbono y sus facturas de servicios públicos.
“Requiere algo de inversión”, dijo Vitello sobre los costos del nuevo equipo. “Pero la inversión retorna. Mi consejo sería que cualquier pequeña empresa lo investigara con su contratista o su electricista. Hagan números. En la mayoría de los casos, calcularía que se amortiza muy, muy rápidamente”.
La empresa también tiene previsto mantener el impulso. Su próximo gran proyecto: Instalar paneles solares en el tejado que generen energía limpia para la fábrica. “A largo plazo, nos gustaría que nuestras operaciones de fabricación fueran básicamente de cero emisiones de carbono”, dijo Vitello.
“Al ser una empresa centrada en productos respetuosos con el medio ambiente, queremos hacer todo lo que podamos en nuestras operaciones de fabricación para ser lo más ecológicos posible. Lo que me encanta del programa es que es bueno para tu negocio y también para el planeta”.
Descubra cómo Energy Trust puede ayudarle a actualizar los equipos de su empresa industrial en www.energytrust.org/paranegocios/fabricacion-pequena.