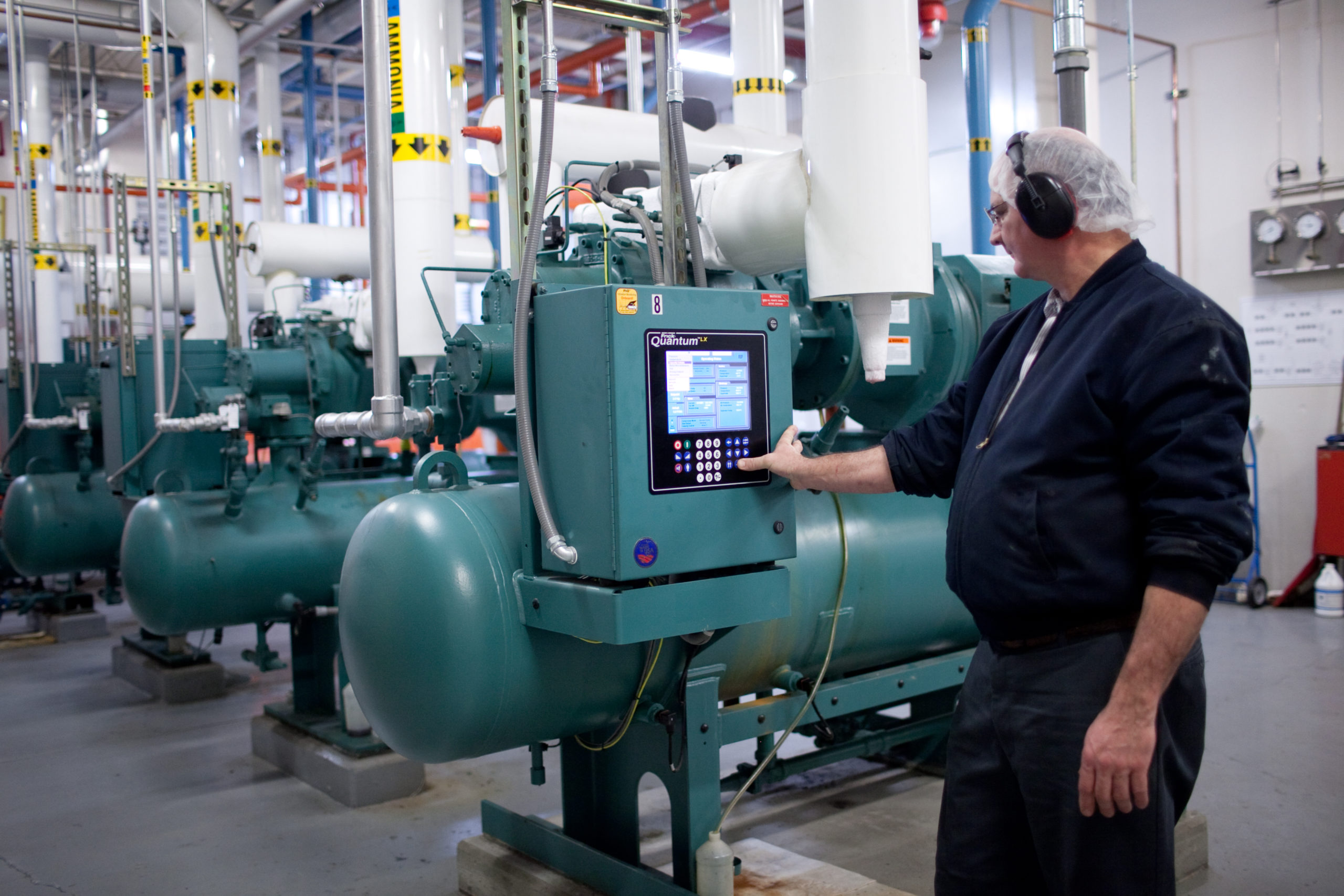
By reducing energy consumption, you can control operating costs and save money. Power your bottom line with these energy-saving tips and upgrades.
Energy Trust of Oregon offers cash incentives to help lower the cost of energy-efficient equipment upgrades. Cash incentives may be available for equipment upgrades marked with an asterisk (*).
- Install occupancy or vacancy sensors in areas with occasional utilization to reduce energy use by approximately 25%.*
- Replace office and warehouse fixtures with high efficiency LEDs to reduce energy costs by up to 70%.*
- Reduce air pressure by 2-psi to save up to 1% on energy costs.
- Use 4 to 5 gallons of receiver capacity for each cfm of compressor capacity to operate load/unload control systems effectively.
- Use a variable frequency drive (VFD) when operating under a partial load to save more energy overload/unload or modulation controls.
- Tag and repair leaks on a regular basis to reduce total compressed air use by up to 30%.
- Reduce motor load to gain more effective energy savings.
- Rewind your motors for maximum efficiency. Contact a member of the Green Motors Practices Group, www.GreenMotors.org, for more information.
- Utilize software like MotorMaster+ to quickly select and manage efficient motors.
- Replace a throttle valve or bypass valve with a VFD to control flow.*
- Use a VFD to regulate flow instead of inlet guide vanes and dampers to save on energy costs.*
- Replace radial-tip and material handling fans with airfoil fans to increase efficiency.*
- Reduce fan speed by 10% to save approximately 25% on energy costs.
- Raise water temperature to increase chiller efficiency.*
- Install an energy-efficient chiller to reduce energy use by approximately 50%.*
- Reduce condenser water temperature by 1°F to increase energy efficiency by 2%.
- Install a VFD on chillers, pumps and cooling tower fans to reduce energy consumption.
- Install high-speed doors in refrigerated areas to reduce energy waste.*
- Install occupancy or vacancy sensors on lighting in refrigerated areas to reduce heat gain from the lights.
- Increase compressor suction temperature by 1°F to save up to 2% on energy costs.
- Decrease saturated condensing temperature by 1°F to save up to 1.5% on energy costs.
Talk with Energy Trust to take the next step to save money and improve the efficiency of your operations. Call 1.866.202.0576, email production@energytrust.org or visit www.energytrust.org/industry.