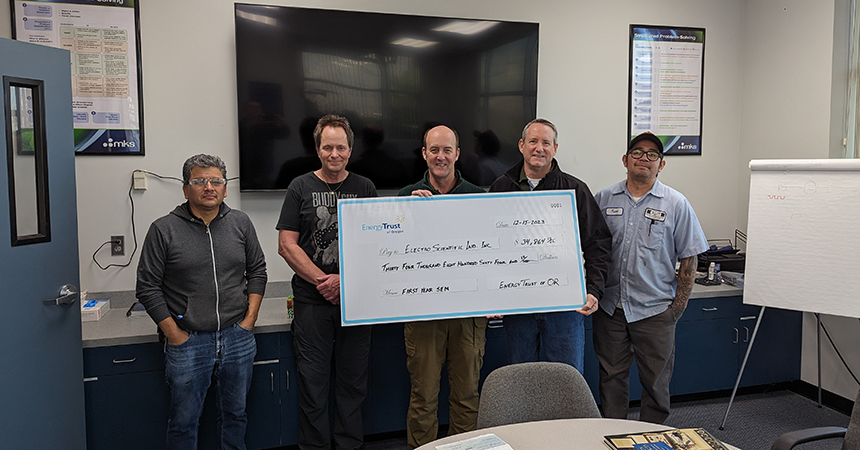
ESI in Klamath Falls, a wholly owned subsidiary of MKS Instruments, manufactures a silicone rubber carrier plate that holds multilayer ceramic capacitors during their manufacturing process. ESI’s product is used by high-volume chip producers.
When Scott Cole took over as plant manager at ESI in Klamath Falls, he’d been with the company for more than 20 years, but was new to facilities and operations. On top of that, he had to hire a new maintenance technician. The team was in learning mode, and it didn’t take long to recognize that some of the equipment and systems were functioning inefficiently—or not at all.
“I was working with a contractor to fix our air handlers, and he pointed out several other interrelated systems that weren’t up to speed, such as the building management system,” said Cole. The contractor was still on site and his input was fresh in Cole’s mind when Energy Trust of Oregon stopped by to talk about Strategic Energy Management (SEM)
When Cole learned that SEM helps industrial facilities identify high-impact energy-efficiency projects, while also developing employee skills to evaluate and manage energy for long-term savings, he said yes.
“I wanted to make operations improvements to reduce energy consumption and costs.” SEM seemed like a great way to make that happen.
One of the first SEM steps is a walkthrough assessment of the facility, called a Treasure Hunt. Energy Trust’s SEM Coaches and engineers joined ESI’s energy team—which consists of Cole plus the site’s engineer, machinist, maintenance technician and a production representative—for a few hours walking through the facility to identify a list of project opportunities. After prioritizing the list of project opportunities with support from the SEM team, Cole delegated projects to the team and an electrician.
In the first year of SEM participation, ESI completed more than 70 projects that cut energy consumption by an annual estimate of 17.6% and added up to an estimated 797,000 kilowatt hours and $60,000 in annual energy savings.
“It was phenomenal and even more than our initial goal of 15% over five years!” Cole said. “Plus, we received $32,000 in cash incentives from Energy Trust for our efforts. Those results help a lot in selling additional energy-efficiency projects to HQ, like the new variable frequency drives we’re installing now.”
Many opportunities throughout the facility
The 60,000 square-foot facility is primarily production space housing machinery with a total site staff of 27. ESI’s process involves drilling thousands of holes in the carrier plate, which is then over-molded with silicone rubber. The injection molding machine has to be continually chilled, so ESI’s manufacturing relies heavily on cooling equipment. As the primary energy user in the facility, the HVAC system was one logical place to focus SEM efforts.
“Our building management software system was obsolete and not really functioning—so it seemed like the equipment that wasn’t broken, plus all redundant systems, were on and running at full speed all the time,” said Cole. Ideally the management system would cycle between the three boilers and two pumps to even out operating hours and wear. The new software is partially installed and with the assistance of the SEM coach, ESI reprogrammed the boiler set points and rotation to improve energy efficiency.
The SEM team identified that ESI’s chilled water system had several components that needed attention. The variable frequency drives (VFD) on the two condenser water pumps and the four chilled water pumps were all broken, so all were functioning at maximum output instead of regulating water based on demand load. With the expert guidance of the SEM coaches and engineers, ESI figured out how to rotate the pumps to level out energy use and eliminate redundancy. The company is in the process of replacing the VFDs and will receive cash incentives from Energy Trust for those too.
Back when the equipment failures in the condenser water loop first happened, before ESI started their SEM engagement, the company had temporarily realigned the system to maintain production. This change unintentionally increased water temperatures to the chiller during the summer, which degraded system capacity and performance. When the SEM team reviewed operations and identified this opportunity, ESI replaced the failed equipment and realigned the system for optimal performance.
The cooling tower fans offered energy-efficiency opportunities too. The software had been set up to switch between two fans, one high speed and one low. When the low-speed fan broke down the high-speed fan took over full time, increasing energy use and providing more exhaust/airflow than needed. ESI opted to add a VFD on the high-speed fan rather than repair or replace the low-speed model, which resulted in more efficiency in the system.
As the SEM team continued to explore ESI’s operations, they saw the cooling tower make-up water valve had been stuck in the open position sending water down the drain for over a year. By repairing the valve, ESI cut its water use in half for the entire plant!
Big savings are in the air
Like many manufacturing facilities, ESI utilizes compressed air in its processes. Cole knew that these systems are prone to leaks, but didn’t realize the cost until they discovered nearly 80 leaks during an Energy Trust compressed air leak repair sweep, similar to a Treasure Hunt and a regular part of SEM . ESI has fixed nearly all of the leaks, and purchased their own leak detection system. “You have to stay on top of it. New leaks spring up,” said Cole. ESI also sequenced its air compressors so that the standby compressor idles until it is called on to relieve the other one. Nearly 90 leaks were identified and fixed over the course of two years, which amounts to annual energy cost savings of approximately $25,000.
Many of the opportunities that result from SEM are simple and low-cost, like turning off machinery when it is not in use. ESI found several areas where this made a difference, including:
- Turning off heaters in the chemical shed and chiller/compressor rooms for the summer.
- Turning off molding machine heaters at shift’s end.
- Programming drilling machines to turn off automatically after a sequence, often during the night.
- Rewiring exhaust fans to turn on or off with their associated machines.
ESI is looking ahead to even more savings from the changes they’ve made and is budgeting for new projects and equipment with help from Energy Trust. “SEM has opened our eyes to things that were not on our radar, like powering down machines at night, fixing leaks or mapping energy use,” said Cole. “Before, we only focused on orders, staffing and raw material cost. We were not thinking about the underlying cost of building operations and infrastructure. Now we do, and know how to manage it better.”
If you would like to learn more about Strategic Energy Management and if it’s a good fit for your facility, contact Energy Trust at 1.866.202.0576 or production@energytrust.org to connect with our team.