When A-dec, a leading dental equipment manufacturer based in Newberg, Oregon, set out to improve the energy efficiency and environmental impact of its operations, the goal wasn’t just to save on utility bills—it was to transform its manufacturing processes. With support from Energy Trust of Oregon, A-dec launched a project that replaced its traditional metal pretreatment process with a safer, lower-energy solution. Energy Trust was pivotal in moving the project forward, covering over 70% of the total project costs, including over $83,000 in incentives. The results have exceeded expectations, delivering significant energy savings, waste reduction, and long-term business value. A-dec now saves an estimated 457,000 kilowatt-hours of electricity and over 4,800 therms of natural gas each year – over $39,000 in annual cost savings. According to A-dec, it also eliminated hazardous waste streams, saving approximately $200,000 annually in disposal costs.
A-dec has been designing and manufacturing dental chairs, cabinetry, lights and equipment for over 60 years. Its reputation for quality and reliability is well established. Yet the company recognized that even the best legacy processes could be improved, especially when they involve high energy consumption and chemical waste.
The original pretreatment method, which involved zinc phosphate and chromate conversion, was energy-intensive and required heating chemical tanks to 175°F. This not only drove up energy usage but also generated chemical waste that cost hundreds of thousands of dollars in disposal each year. While the company maintains robust health and safety protocols, the nature of these chemicals will always pose some level of risk to employee safety when disposing of chemical waste.
When a forward-thinking A-dec engineer returned from a metal pretreatment conference with bold ideas to improve efficiency and reduce hazardous waste, they needed data to prove the value of change. That’s where Energy Trust came in, providing the technical insight and cost analysis to validate a switch to zirconium oxide—a safer, lower-energy alternative that sets the stage for broader process improvements.
Working together, A-dec and Energy Trust teams tested and validated the project. The company needed assurance that the new process would maintain its product quality standards—especially since its equipment is designed to last 20+ years in clinical environments. Engaged early in the process, Energy Trust engineers worked closely with A-dec to analyze energy savings potential, refine the project scope, and structure incentives. This guidance was instrumental in scaling down an initially ambitious $7.5 million plan into a manageable first phase—focused on switching to the new pretreatment chemistry.
These positive outcomes are matched by other significant non-energy benefits. The risk of exposure to chemicals and waste streams is essentially eliminated with the process improvement. The facility’s air quality has improved, and operations are at or near room temperature, considerably enhancing workers’ comfort. “The entire space is significantly more comfortable than before, much less hot and humid,” notes Dustin Harper, Staff Manufacturing Engineer at A-dec.
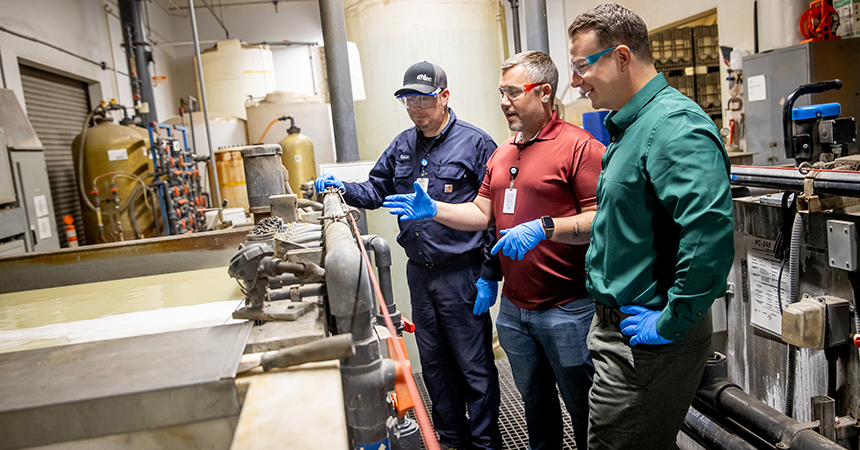
The project team comfortably walks through the pretreatment process, in what was previously a hot and humid environment
Additionally, the new process sets the stage for future innovation. Because zirconium oxide is compatible with more advanced spray wash application systems—rather than traditional dip tanks—A-dec is now positioned to save money while maintaining the highest standards. The new process allows them to reclaim expensive coating materials, improve throughput, and further reduce resource consumption.
According to A-dec leadership, the success of this project has created “street cred” internally, demonstrating that ambitious sustainability projects can be executed without compromising quality. Future plans include upgrading the powder coating process to capture and reuse excess material, with projected savings of a quarter-million dollars annually.
The partnership with Energy Trust has been critical throughout the process. From early engagement to on-site technical evaluations and incentive development, Energy Trust provided not just funding but confidence. Having a third-party validate the energy and cost savings added credibility to internal pitches and helped drive executive support.
“When you’re making significant changes like these, it can’t be overstated just how important it is to have a coalition of good partners internally, and externally,” Harper says. “Energy Trust played a vital role in our ability to improve.”
Key project results include:
- Received $83,773 in Energy Trust incentives, 71% of the total project costs
- $39,960 in annual energy savings
- 457,000 kWh/year in electricity savings and 4,837 therms of gas saved
- $200,000/year saved from the elimination of chemical waste, according to A-dec
- Enhanced workplace safety
- Long-term readiness for future sustainable manufacturing upgrades
Ultimately, A-dec’s success proves that forward-thinking manufacturers can align efficiency and environmental impact reductions with core business goals. By investing in energy-smart technologies and leveraging Energy Trust’s resources, A-dec has not only reduced its energy use but also boosted operational resilience while retaining product integrity.
Learn how Energy Trust can help your industrial facility save on energy costs.
You can also reach our team directly to answer any questions you have. Give us a call at 1.866.202.0576 or email at production@energytrust.org.