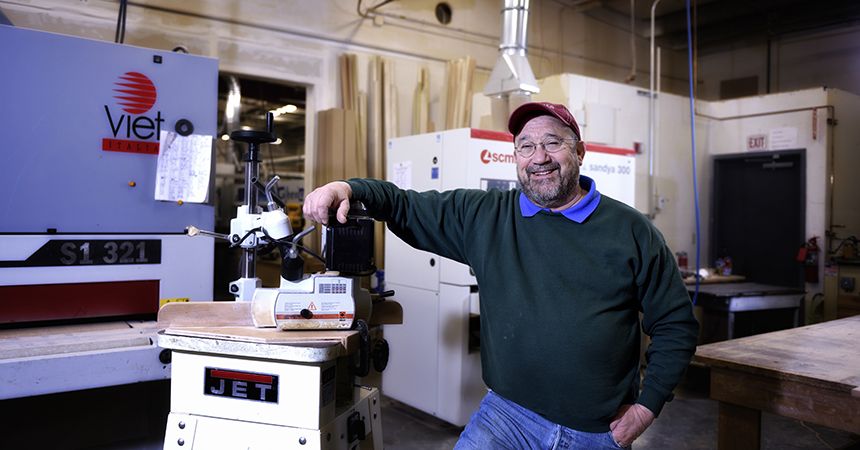
When Robin Chester of Chester Cabinets pulled up to his shop in Bend, Oregon, during his employees’ lunch breaks, he could hear the dust collector system running even though no equipment was in use. “I knew that was not right and it had gone on for years,” he said. While dust collectors are critical in woodworking facilities to improve air quality and reduce fire hazards from wood processing dust and particulates, Chester recognized that tying dust collector operation to equipment operation could save both energy and money.
Seeking solutions
At a cabinet manufacturing trade show, Chester saw products that turned on the dust collector when the machinery turned on and turned off the dust collector shortly after the machinery turned off – the type of solution he was seeking to cut back his dust collector system’s daily operation. He soon learned that reducing his energy use might qualify for incentives from Energy Trust of Oregon.
While touring the facility, an Energy Trust energy analyst recommended measuring run-times for each of the seven pieces of equipment connected to the current dust collector system; this information would provide a baseline for determining energy savings from the dust collector system upgrade.
Tool Lending Library delivers energy measurement devices
Energy Trust helped Chester borrow the requisite measurement devices – motor run-time loggers – from the Tool Lending Library. The Tool Lending Library is a free service that lends diagnostic tools to Energy Trust customers to monitor equipment and identify projects to reduce energy use. Energy Trust encourages customers to utilize the Tool Lending Library to monitor their energy use but it’s a not a requirement for completing an efficiency project. The energy analyst can provide all the needed technical services and tools.
“I contacted the Tool Lending Library and lo and behold, seven little loggers showed up in the mail,” said Chester. “After the energy analyst programmed the motor run-time loggers, they magnetically attached to the equipment motors and tracked when each machine was running.”
Little data loggers identify big opportunities for energy savings
The loggers collected run-time data for two weeks. Analysis of the data for all seven motors indicated that the dust collector could be turned off for two out of nine hours per day.
Chester Cabinets worked with an Energy Trust trade ally who upgraded and consolidated the dust collector system, installing new custom controls to link the dust collector’s operation to equipment operation. The controls for the upgraded dust collector system recognize that if all seven pieces of equipment have been off for three minutes, it should turn off the dust collector. Then it stays off until one of the seven pieces of equipment turns on again.
“Originally, machine run-times didn’t matter to the dust collector; it ran all the time,” Chester said. “Now the machines still run the same, but the dust collector doesn’t.”
The project has already produced substantial reductions in energy use. Annually, Chester may save an estimated 33,700 kilowatt-hours through reduced dust collector run-time and 3,000 therms through the decreased need to heat makeup air during colder months. “My electric bill is approximately $400 less each month and the remaining return on investment was recouped within a year,” said Chester.
The project cost Chester about $16,000. “To put the icing on the cake,” he said, “it was determined that I saved enough on energy that I qualified for a check for $11,000 from Energy Trust. That’s huge. It was a very quick payback.”
“It went really smoothly,” Chester continued. “The Tool Lending Library was easy to deal with and Energy Trust’s energy analysts has a wealth of information. They spend time with you and share what other people are doing and how it seems to work for them. I’m pretty happy with it all. And the system works great.”
To learn how you can get the most out of your facility’s equipment connect with an Energy Trust energy analyst, email production@energytrust.org or call 1.866.202.0576.