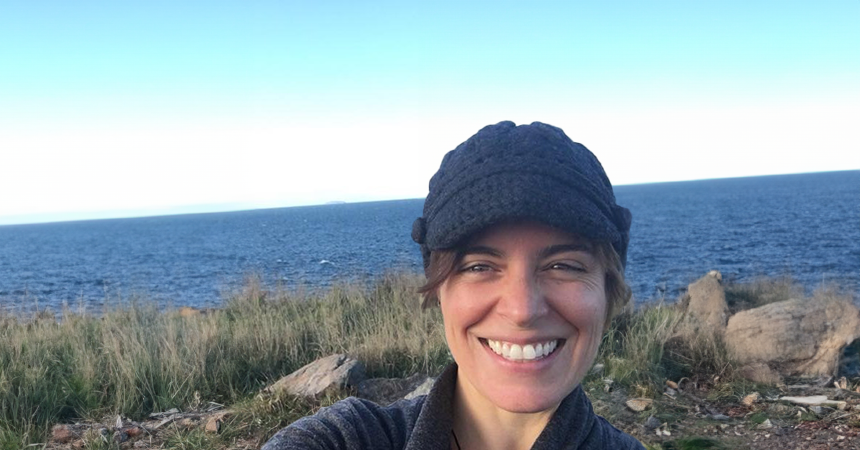
This is a part of a series of blog posts amplifying community voices.
Karen Rugg’s longtime interest in sustainability and the built environment led her to get a master’s degree in city and regional planning, focusing on real estate development and sustainable affordable housing. She later transitioned into commercial construction, where she attained LEED accreditation and began implementing ways to make projects, jobsites and office operations more sustainable. After moving to Bend in 2018, she co-founded Perennial Building with her partner Ashley Bice and soon began developing a mixed-use project in downtown Sisters, Oregon that will use hempcrete as a primary building material.
Q: What drew you to commercial construction as a career?
From a young age I was interested in sustainability, the built environment and our place in it. I worked in city planning for a year after getting my masters, which was a great experience and allowed me to explore my interest in sustainable community planning, but ultimately, I found that I wanted to be more involved with building. It was more tangible for me. The challenge of large-scale projects and the opportunity to make a significant impact was what drew me to commercial construction specifically.
Q: How does the natural world play a role in your work?
There is a lot we can learn from the natural world and the more we use its intelligence in design, the better off we’ll be. At Perennial Building, our main focus is building with hemp-lime, also known as hempcrete. Hemp is as natural and renewable as a building material can be and has characteristics that make it far superior to address the environmental and health issues we face today.
Q: You’ve been an early advocate in Central Oregon for using hemp in the built environment. Why hemp?
Hempcrete is made with hemp and lime — two natural materials that when combined together check all the boxes. It can be up to 70% more energy efficient than traditional construction; it’s renewable, nontoxic and sequesters carbon for the life of the building; and it is resistant to fire, insects and mold. The fire resistance of hempcrete alone is a great reason to build with it in our region. It not only insulates but has thermal mass, creating a dynamic environment that regulates interior temperature and humidity levels. It can also improve air quality in a building. Then at the end of its useful life, estimated at 100 years by some sources, it can be composted. I also think it has the ability to scale because it can be incorporated into any type of architectural style. For us, it’s a no brainer to build with hempcrete.
Q: Tell us more about the mixed-use building you’re planning to build in downtown Sisters .
My partner and I have spent two years developing a mixed-use hempcrete building for downtown Sisters. We have coordinated with Deschutes County to address their questions around life safety and structural soundness and conducted independent research scale ASTM E119 fire testing on our hempcrete wall assembly which passed with flying colors. The land is purchased, the design is complete, and our next step is to secure funding for the construction. We hope to break ground in spring 2025.
It will be a small boutique hotel and a flagship in the PNW for introducing hempcrete to more people. That is the goal with this first project, to provide an opportunity for people to fully experience hempcrete and increase awareness and demand. To learn more about the project or get involved, people can visit www.perennialbuilding.com.
Our ultimate goal is to build hempcrete homes and make them as affordable and accessible as possible. Affordable housing is often made with toxic, cheap materials, and the negative health impacts of those materials are well documented and can be significant. Healthy homes shouldn’t be a luxury, but a given starting point.
Q: What excites you about your work?
There is a lot of innovation in the natural building material space right now. We are at this nexus of the climate crisis, advanced technology and renewed interest in biogenic materials. It gives me hope that we will find simple yet elegant solutions to build better while simultaneously having a positive impact on people’s lives and the planet.
Q: What do you see as the biggest challenges in advancing sustainability efforts in construction?
Lack of awareness and affordability are challenges. We need to raise awareness of natural building options, such as hempcrete, which in turn will drive demand, and can make supply chains more robust and reduce costs. Because of legal reasons, hemp couldn’t be grown in the U.S. until recently in 2018, so the supply chain is in its early stages. Even so, its cost per square foot is already comparable to conventional construction depending on project specifications. We need to continue this trajectory and make these options within reach. Fortunately, hempcrete was recently approved for the IRC and the commercial building code is being developed right now. This will make it more accessible for architects to specify.